Troubleshooting Your Equipment: When to Call for Packaging Machine Repair
Troubleshooting Your Equipment: When to Call for Packaging Machine Repair
Blog Article
Quick and Reliable Product Packaging Equipment Repair Service Solutions to Minimize Downtime
In the competitive landscape of manufacturing, the effectiveness of product packaging operations hinges on the dependability of equipment. Quick and reliable repair service solutions are important in alleviating downtime, which can lead to substantial financial losses and operational obstacles.
Value of Timely Services
Timely repairs of packaging devices are important for preserving functional performance and lessening downtime. In the hectic atmosphere of production and packaging, even small malfunctions can lead to significant hold-ups and performance losses. Resolving concerns without delay makes sure that machines operate at their optimal capacity, therefore securing the flow of procedures.
Additionally, timely and routine maintenance can prevent the rise of small troubles right into significant breakdowns, which frequently incur greater repair service expenses and longer downtimes. A positive method to machine fixing not just protects the integrity of the tools however likewise enhances the total dependability of the assembly line.
In addition, timely repair work contribute to the durability of packaging machinery. Devices that are serviced immediately are less likely to struggle with excessive damage, permitting services to maximize their financial investments. This is specifically vital in sectors where high-speed product packaging is vital, as the requirement for constant performance is critical.
Benefits of Reliable Service Providers
Dependable provider play an essential duty in making sure the smooth operation of product packaging devices. Their knowledge not just enhances the effectiveness of fixings but additionally adds significantly to the durability of tools. Dependable solution carriers are geared up with the technological expertise and experience required to detect concerns accurately and execute effective solutions rapidly. This minimizes the threat of recurring problems and ensures that devices operate at ideal efficiency degrees.
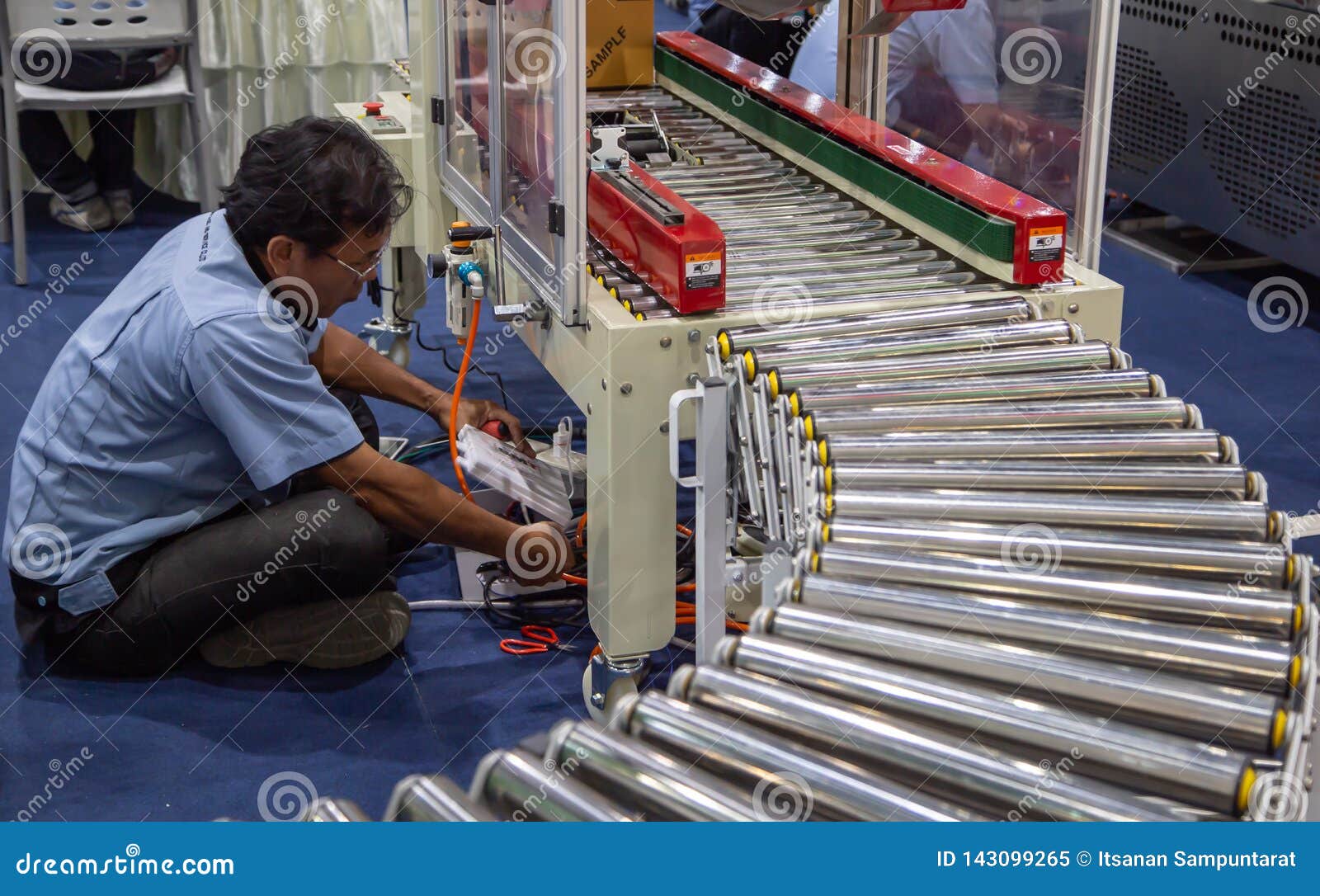
In addition, a trustworthy company offers comprehensive support, including training and guidance for team on machine operation and maintenance ideal techniques. This not just encourages staff members but likewise cultivates a culture of safety and efficiency within the company. On the whole, the advantages of engaging reputable solution providers expand past instant repair work, favorably influencing the whole functional workflow of product packaging processes.
Typical Packaging Maker Problems
In the world of packaging operations, various issues can jeopardize the effectiveness and performance of equipments (packaging machine repair). An additional common problem is misalignment, which can cause jams and irregular product packaging, influencing item top quality and throughput.
Electrical issues can also interfere with packaging operations. Damaged wiring or malfunctioning sensors might lead to irregular maker behavior, causing delays and boosted functional costs. Furthermore, software glitches can impede the equipment's programming, bring about operational ineffectiveness.
Irregular product flow is an additional crucial problem. This can emerge from variants in product weight, size, or my blog shape, which may affect the maker's capability to handle things properly. Lastly, not enough training of operators can intensify these issues, as inexperienced employees might not identify very early indicators of breakdown or might misuse the equipment.
Dealing with these common packaging machine issues promptly is necessary to preserving productivity and guaranteeing click to read more a smooth procedure. Normal assessments and positive maintenance can considerably reduce these issues, fostering a trusted product packaging environment.
Tips for Reducing Downtime
To minimize downtime in product packaging procedures, executing a positive maintenance strategy is crucial. Routinely set up upkeep checks can identify possible issues before they rise, guaranteeing machines run effectively. Developing a routine that includes lubrication, calibration, and inspection of essential elements can dramatically decrease the regularity of unforeseen failures.
Educating team to operate machinery properly and identify early indication of malfunction can likewise play a vital duty. Empowering drivers with the knowledge to perform standard troubleshooting can avoid small issues from triggering major delays. In addition, preserving a well-organized supply of vital extra parts can accelerate fixings, as waiting for parts can cause extensive downtime.
Additionally, documenting equipment efficiency and maintenance tasks can help identify patterns and recurring problems, enabling for targeted interventions. Including innovative tracking modern technologies can provide real-time data, enabling predictive maintenance and lessening the danger of unexpected failings.
Lastly, promoting open communication in between operators and upkeep teams guarantees that any kind of abnormalities are promptly reported and dealt with. By taking these aggressive steps, companies can improve operational effectiveness and dramatically lower downtime in product packaging procedures.
Picking the Right Repair Solution
Selecting the appropriate repair solution for packaging equipments is an essential choice that can considerably influence operational performance. Begin by examining the company's experience with your specific kind of packaging devices.
Following, take into consideration the company's online reputation. Seeking responses from other organizations within your industry can offer insights right into dependability and top quality. Accreditations and collaborations with recognized devices suppliers can likewise show a commitment to excellence.
In addition, evaluate their feedback time and availability. A solution company that can click this link supply prompt assistance minimizes downtime and maintains production circulation constant. It's also critical to ask about service warranty and service assurances, which can show the self-confidence the service provider has in their job.
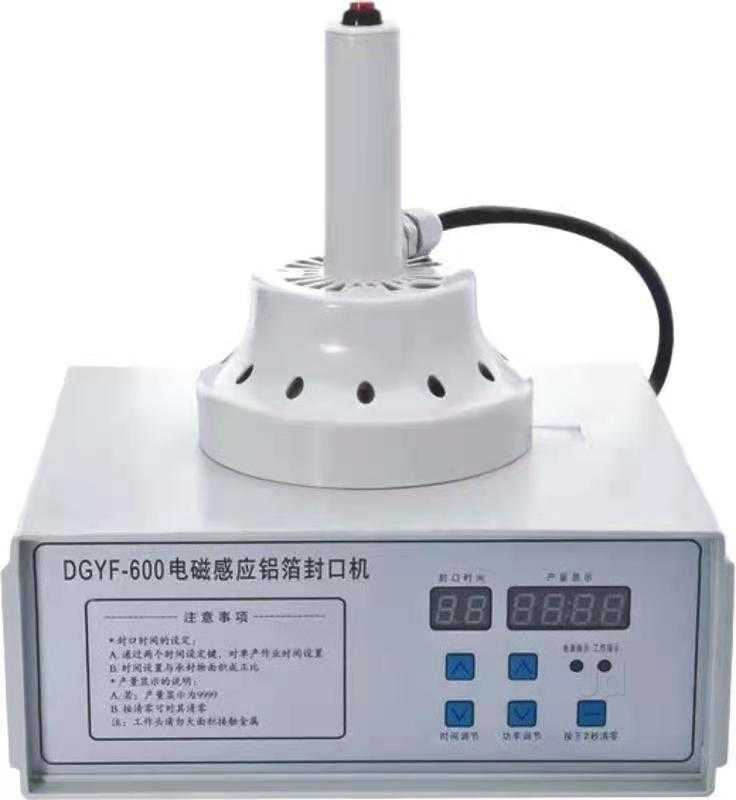
Verdict
In verdict, the value of trusted and quick packaging maker repair services can not be overstated, as they play a critical role in lessening downtime and ensuring operational effectiveness. Applying aggressive maintenance practices and investing in personnel training further improves the durability of product packaging equipment.
Prompt fixings of packaging machines are important for keeping functional performance and minimizing downtime.Additionally, timely repair work contribute to the durability of packaging machinery. In general, the benefits of engaging reputable service suppliers prolong beyond instant repair services, positively affecting the entire operational process of packaging procedures.
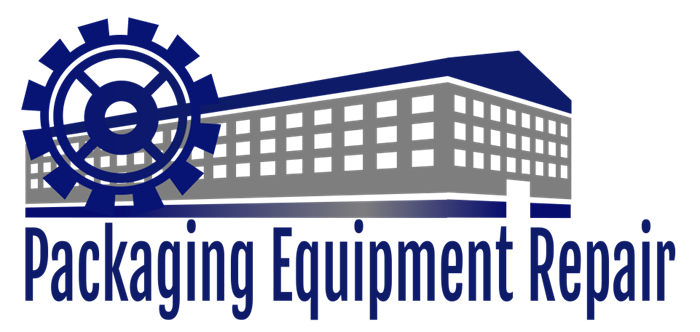
Report this page